提高筒类锻件表面质量的措施
2020-12-22 16:41:02
浏览次数:
筒体锻件是压力容器中重要的组成部分,筒节质量的好坏直接关系到整台反应器的好坏。由于筒节大部分都需要镦粗冲孔、芯棒拔长、扩孔等工序 ,所以在生产过程中容易出现飞边、折伤、椭圆等质量问题而导致锻件报废。本文结合筒类锻件的生产工序分析总结了筒类锻件的几种质量问题,针对这几种质量问题提出了解决方案以及预防措施。
1、筒类锻件的几种质量问题
通过长期的生产跟踪,筒类锻 件容易出现以下几种质量问题:
(1) 内外表面出现凹坑、折伤;
(2) 端面长短不齐、壁厚不均匀;
(3) 筒节端面出现折伤以及飞边开裂、飞边折叠进入筒身内部;
(4) 出成品后椭圆度较大。
2、 产生质量问题的原因
2.1 筒身内外表面出现凹坑的原因是:锻件在炉内长时间高温加热,自身产生较厚的氧化铁皮,锻造前没有用合适的方法彻底清除氧化皮,锻造过程中将较厚的氧化皮压人锻件本体造成凹坑;坯料与加热炉垫铁上的氧化皮粘连,锻造前同样是由于没有用合适的方法去除,导致氧化皮压入锻件本体。
2.2 内外表面产生折伤主要是由于锻造过程中锤与锤的搭接量以及压下量存在问题所致。
2.3 锻件出现长短面主要存在于有拔长工序的筒节。长短面的产生主要有以下两方面原因:由于料温不均,在芯棒拔长过程中温度高的地方比温度低的地方走料快而造成端面长短不齐;坯料在芯棒拔长过程中旋转角度太大造成漏锤,再加上每一锤 的压下量不同,最后导致产生长短面。
2.4 筒节壁厚不均主要是由于坯料冲孔冲偏后,在芯棒拔长和扩孔出成品时没有及时的调整压下量所致。
2.5 锻件端面出现折伤、飞边开裂以及飞边折叠进入筒身内部主要是由于冲孔工序造成。折伤的产生是由于在没有设计专用漏冲脱附具前,漏冲脱采用两个平台相互配合,坯料端面和大小平台接触处产生勒痕,坯料勒痕处在芯棒拔长或马杠扩孔过程中逐渐演变成折伤。飞边开裂和飞边折叠进入筒身内部主要是由于冲孔后毛刺没有得到及时的处理,在后序芯棒拔长和马杠扩孔过程中逐渐产生。
2.6 锻件产生椭圆有以下几方面原因:锻件出成品火次保温时间太长,导致将坯料烧成椭圆,在扩孔出成品时没有及时的将椭圆校圆;出成品后终锻温度太高,成品摆放不当,由于锻件 自重造成椭圆;扩孔出成品时压下量不均匀,变形不同步造成成品椭圆。
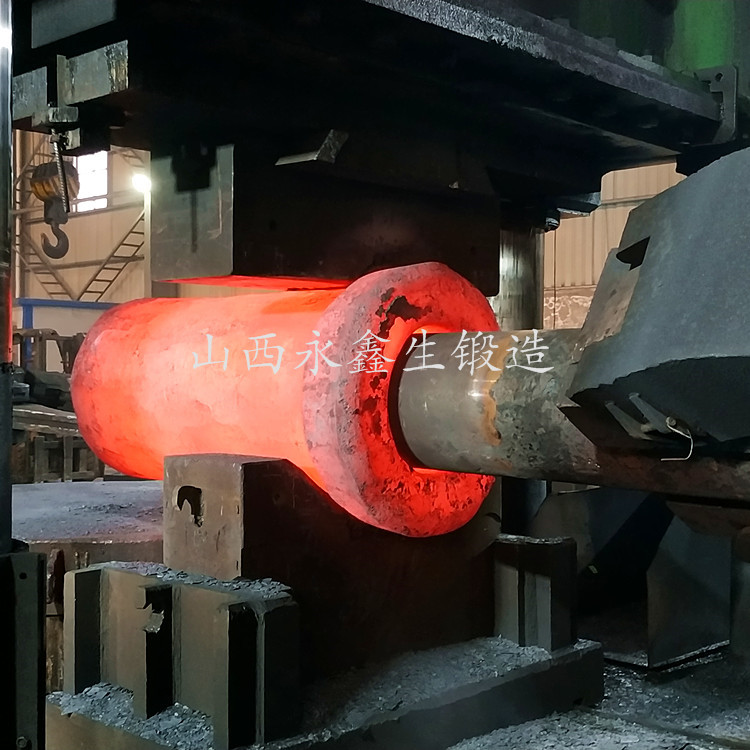
3、 解决方法及预防措施
3.1 为了避免氧化皮造成的质量问题采取如下措施:在加热垫铁上铺石棉毡,阻断坯料与加热垫铁上氧化皮的粘连,但是高温状态下在垫铁上铺石棉毡比较困难同时容易造成石棉毡浪费,这种方法适合于重点产品;利用特种吊钳的结构特点,待筒节放置在马架上后,将特种吊钳合抱在筒节有氧化皮的部位,操作车夹持马杠反复旋转,带动筒节旋转将粘连的氧化铁皮刮下。
3.2 为了避免由于料温不均造成筒节在芯棒拔长时出现长短面和坯料被烧成椭圆的情况,可以采用将坯料保温一定时间后,旋转一定角度再进行保温。
3.3 为了从根本上解决筒节端面折伤、飞边开裂以及飞边折叠进入筒身本体等质量问题,采用以下措施:设计专用漏冲脱附具彻底避免端面折伤的产生;坯料冲孔(芯棒拔长)结束后采用吹氧(气割)的方式将飞边彻底清除。
3.4 筒节出成品后由于自重将会使椭圆度增大, 所以采用立料装置将出成品后的筒节竖立放置。
3.5 相对进给量和单道次压下量是锻造时的重要参数,相对进给量b/h(b为 宽;h为坯料高度)太小或太大都容易产生折伤,所以锻造时相对进给量应最好满足0.5—0.85。均匀的压下量可以有效地避免壁厚不均、端面长短不齐等质量问题。